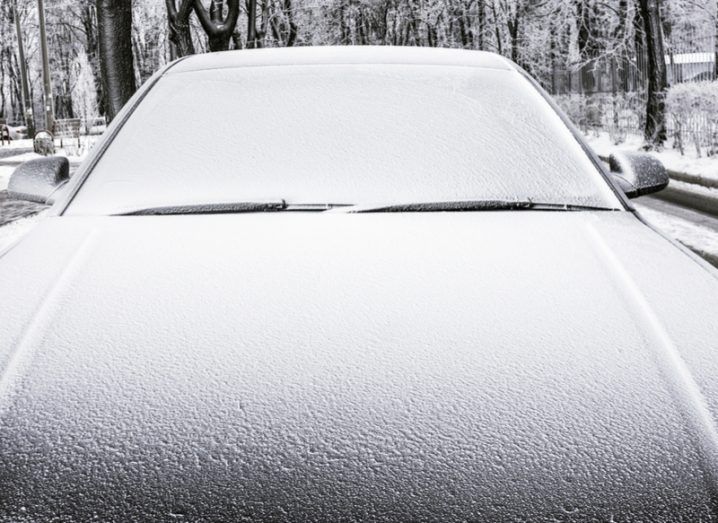
Image: Anna Baburkina/Shutterstock
Defrosting a car windscreen can seem a painfully slow process, but a new breakthrough has found a simple way to cut the time it takes by a factor of 10.
While the more common phrase is that a watched kettle never boils, the same idea could be applied to a car windscreen when you’re eager to get on the road on a freezing winter morning.
So far, the only way to prevent it is to get scraping, or use a store-bought product the night before.
But now, Virginia Tech engineer Prof Jonathan Boreyko has turned this frustration into action. He has developed a new concept that could cut the amount of time it takes for a car’s defroster to work by a factor of 10, using a “very simple chemical recipe”.
Along with a pair of undergraduate students, Boreyko treated some aluminium plates to render them superhydrophobic, meaning that they actively repel water.
When the temperature was brought below zero, the resulting frost on the plates’ surfaces would grow in a “suspended state” so that it was technically not stuck to the car’s window – a process he calls dynamic frosting.
“There were a lot of nano air pockets between the frost sheet and the actual solid substrate of aluminium,” Boreyko explained.
“This made the frost highly mobile and easy to shed as it melted, kind of like a puck on an air hockey table.”
Using a standard window, the frost meltwater will stick to the surface until it is slowly evaporated, making the whole process equally slow.
What’s next for the concept?
Despite the phenomenon of superhydrophobic reactions being well known to science for some time, their ability to form air pockets underneath frost has not been widely explored.
“My idea came from the realisation that frost is simply dew droplets that have frozen over into ice – so, if dew droplets can be highly mobile on a superhydrophobic surface, maybe frost can be, too,” Boreyko said.
“Sure enough, when frost formed on our chilled superhydrophobic aluminium, the ice was able to trap air pockets underneath itself just like with liquid water.”
With this research now published to the journal ACS Applied Materials and Interfaces, Boreyko’s next project will aim to improve upon the chemical mixture so that it is more suitable for long-term use.